Beauport Hotel: Where Historic Charm Meets Modern Coastal Luxury
Located on Pavilion Beach in Gloucester, MA, the Beauport Hotel is a 94-room, full-service destination designed to evoke the elegance of New England’s historic seaside resorts, while delivering every modern amenity expected of a 21st-century event and conference venue.
OLSON LEWIS + Architects was honored to join the Beauport Hotel Design-Build Team, led by Windover Construction with interiors by Niemitz Design Group, contributing more than 35 years of hospitality design experience to this landmark project.
Project Overview
- Client Vision: A modern interpretation of grand North Shore seaside hotels
- Opening Date: June 2016
- Facility: 94 guest rooms, rooftop pool and hot tub, restaurant, bar, grand ballroom, conference/event spaces, and multiple outdoor decks
- Location: Pavilion Beach, Gloucester, MA
The vision for Beauport Hotel was to recall the grand North Shore seaside hotels and summer homes of the past, while providing all the amenity expected in a 21st century event and conference facility.
The initial concept sketches were presented in September 2013, and the Beauport Hotel opened its doors in June 2016. A 94-room full service hotel, Beauport is located on the Pavilion Beach in Gloucester, MA. The architectural feel incorporates a modern American seaside summer cottage feel with clean, light and elegant “beachy” interior finishes.
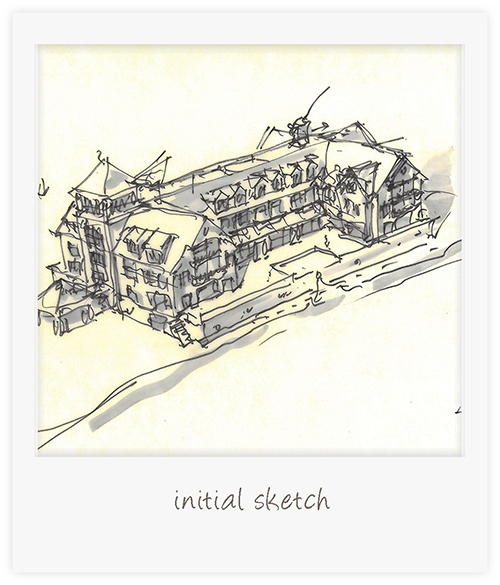
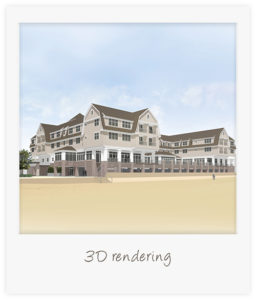
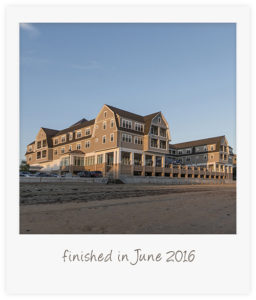
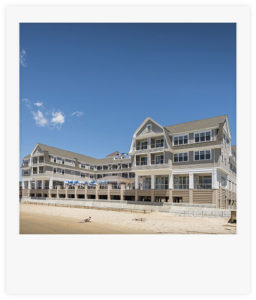
HOTEL SPECIFICS
Exterior | Recalling the resort seaside hotels of the late-nineteenth and early-twentieth century are the gambrel roofline, weathered cedar shingles, copper accent roofing, and expansive wood deck areas at first floor and roof. A waterfront pier-inspired base, and stainless steel cable railings throughout continue the overall nautical theme of the hotel, reinforcing the site’s historic connection to the sea.
Ground Floor Garage Level | The Ground Floor has covered parking for 99 cars and an entrance lobby where the guest can access the first floor via elevators or an inviting staircase open to the lobby above. Outside of the lobby area, the Ground Floor houses an open-air garage with timber screening at the perimeter as a reminder of Gloucester Harbor’s piers and it’s historic connection to the sea. By locating the garage below the hotel, upper floors are elevated for enhanced coastal views. In addition, a loading dock, on-site laundry, valet and security are located on the ground floor.
First Floor Main Lobby & Reception Level | The grand staircase was intentionally designed to locate the opening at the top of the stairs to be situated directly across from the ocean view, thereby setting the stage for the nautical themes for patrons entering the hotel.
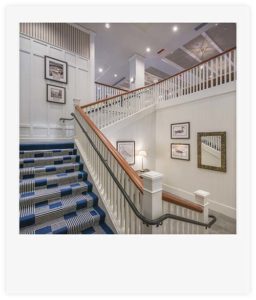
Main lobby, reception area, restaurant and bar/lounge with hardwood floors, wainscoting and light tones on the walls, and crown molding, soffits and light cove ceilings. The lobby reception area and bar have granite tops and wood paneling. The main lobby and bar each feature fireplaces and informal seating areas, for relaxing or meeting with friends. The restaurant features a special private dining room- a perfect spot for enjoying quiet dining and sunset views.
Grand function room/ ballroom and smaller adjacent function rooms continue the design theme of the first floor with similar finishes. The ballroom has its own bar, and can be accessed from the lobby, and pre-assembly space.
The bar/lounge, restaurant and grand function room/ballroom have ocean views through a series of french doors, which can be opened up to create an open-air access to the adjacent deck with a panoramic beach and harbor view for dining, cocktails and functions. Lounge and restaurant style seating surround a fire pit. A generous, centrally located open pavilion, and smaller shaded areas at restaurant and main ballroom complete the deck.
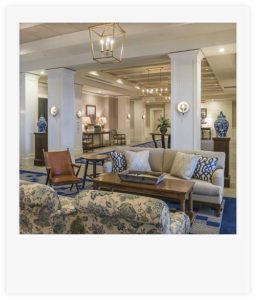
First floor public spaces (event, restaurant and bar & lobby areas) have ornamental coffered ceilings.
The back of house includes the main kitchen to support the restaurant, bar and room service, and also a separate catering kitchen to support the main function room space. There is also an employee break/changing area, mechanical and office space.
Second & Third Floor Guest Rooms | Hotel guests can choose from a variety of room and suite options, and have exclusive use of the rooftop pool and hot tub with a dedicated bar. The guest room levels include 94 rooms with an average size of 380 SF. A mix of room types includes kings, double queens, oversize kings and junior suites. The bedroom décor continues the American cottage theme with carpeting, well-appointed finishes and light wood elements. The bathrooms include glass walk-in showers or tubs, floor and wall tile, and marble vanities. A number of the guest rooms have ocean-facing balconies. There is a fitness room on the second floor.
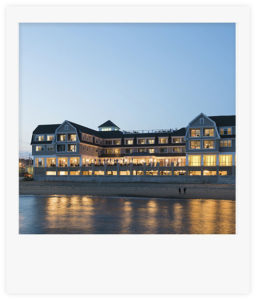
Fourth Floor Roof Deck & tower | The vacant Birds Eye Fish Factory, demolished to make way for the hotel, was located between the inner harbor lobster packing plant on one side, and Pavilion Beach on the other. An iconic tower visible from land and sea rose above everything around it. The client wished to pay homage to this symbol of the working Gloucester waterfront. Olson placed the tower at the heart of the building. Illuminated at night, it houses elevators for use by hotel guests. A toplit rooftop cupola provides access from the elevators below to the deck and pool via an interior vestibule. Access cards allow for separation between the lobby level public spaces and the private spaces on the guest floors and roof deck.
The roof includes space for an outdoor deck and ocean-facing pool and spa, a bar, and space for mechanical equipment. The deck is arranged to provide both ocean and harbor views.
Design Solutions & Challenges
- Coastal Engineering: Flood-resistant concrete seawall, elevated public spaces, hurricane-rated windows and doors
- Custom Prefabrication: Hybrid structural system combining steel, concrete, and prefabricated wood framing, accelerating construction and reducing site congestion
- HVAC Integration: VRF system concealed within interior spaces, maximizing window areas and supporting energy efficiency
- Flexible Event Design: Rooftop pool placement freed valuable first-floor deck space for formal gatherings
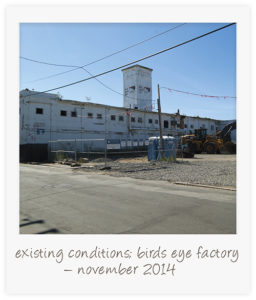
TEAMWORK & CONSTRUCTION
Designing the floor plan within a zoning envelope previously approved by the city of Gloucester presented some challenges, which John and the team at OL+ skillfully overcame. The design/build, fast-track project delivery process required close collaboration between the OL+ and Windover Construction (the hotel’s Design Build Construction Manager).
A hybrid steel/concrete/wood structural system was used to construct the building. The assembly comprises steel framing with concrete slabs at the ground and first floors, and prefabricated wood framing for the second and third floors and roof structure. Steel framing supports the rooftop pool and tower roof. The OL+ team worked collaboratively with all project partners to overcome any obstacles, balancing the needs and concerns of multiple constituents with budget and scheduling constraints.
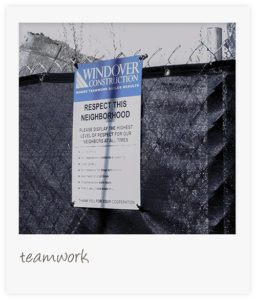
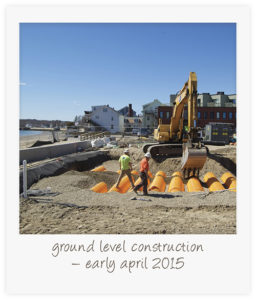
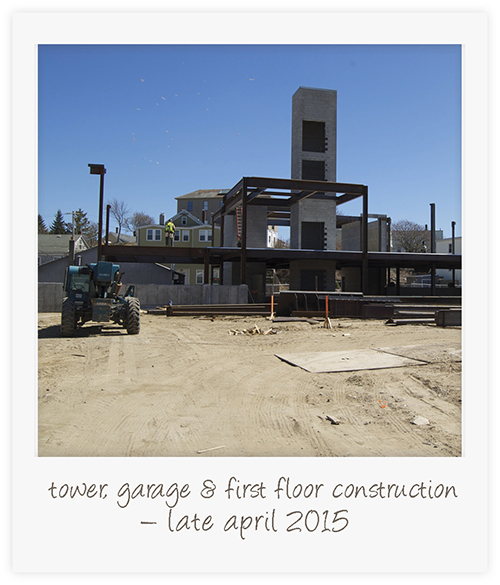
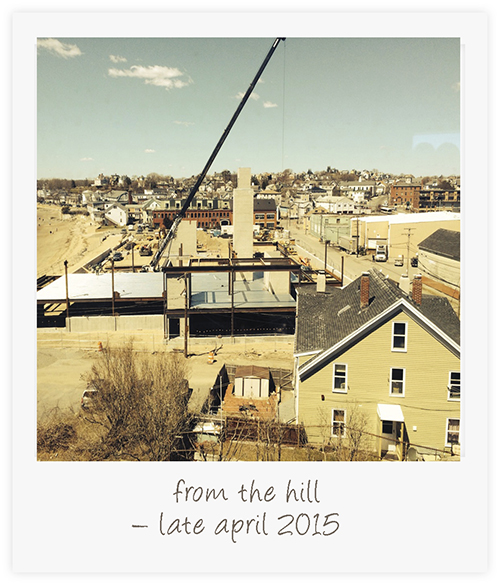
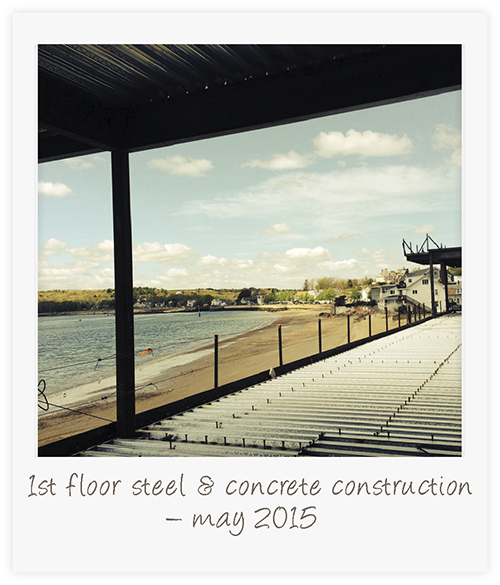
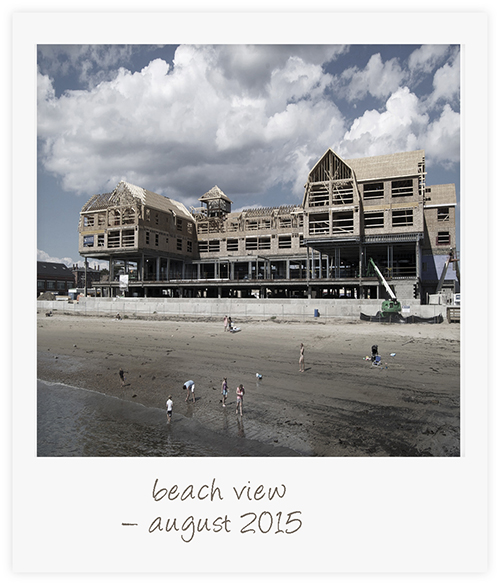

HURRICANE & FLOODING CONCERNS
The coastal Massachusetts waterfront location presented both flooding and hurricane concerns. A concrete sea wall at garage level was constructed to help resist coastal flooding during a storm surge, and primary public spaces were elevated to first floor level. At the first floor deck, ten-foot-high doors and windows were manufactured by a Florida-based company that specializes in impact-resistant coastal applications. In the guest rooms, vinyl-framed impact-resistant windows and sliding doors tested to withstand hurricane-force weather allow plenty of light into the rooms.
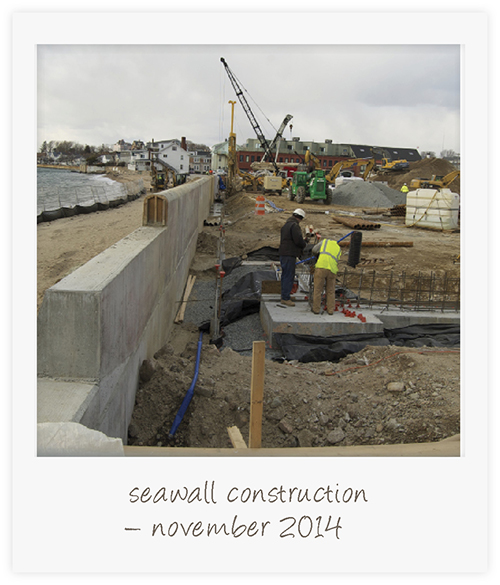
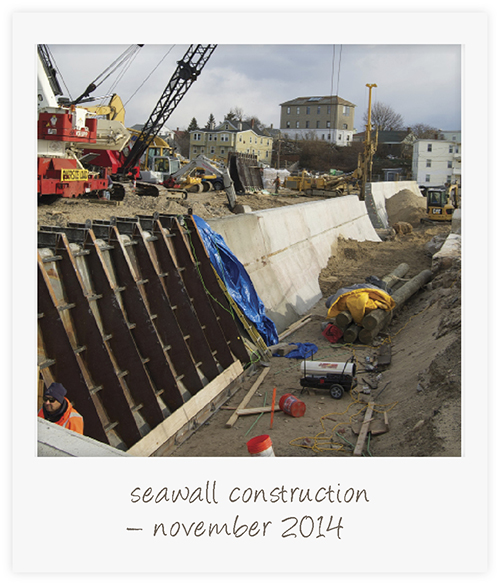

CUSTOMIZED PREFABRICATED CONSTRUCTION
The hybrid construction system employed for the project provided a number of benefits. Off-site construction of the wood framing and roof trusses was vital for keeping the project both on budget and on schedule. The use of prefabricated framing on the upper levels allowed for concurrent sequencing of major structural systems, which would have been impossible using more conventional construction methods.
Second and third floor framing was factory-fabricated while ground and first floor steel was being erected on site. The second floor concrete slab was the first to be poured. The wood framing was erected from the second floor up, while the remaining slabs below were poured. As third floor walls were being erected, roof trusses were fabricated, making them ready to install as walls were completed. Concurrent with this, first floor light-gage metal exterior wall framing, and steel stud interior framing went into place.
The prefabricated wood framing is computer designed to accommodate the irregular shape of the building footprint, gambrel roofs with third floor dormers, and a complex upper roof which is home to an exterior deck with pool, and recessed wells housing mechanical equipment. Prefabrication of the wood framing allowed greater control over the building configuration, and helped reduce construction materials crowding on the very tight Gloucester building site. It was also helpful in limiting construction waste. Throughout the process, the team worked closely with Boise Cascade, the wood framing prefabricator. Boise is a company that adheres to responsible environmental stewardship and sustainability practices, which was important to the entire team.
Guest Floor Construction |Although many of the rooms on the second and third floors are similar, few are exactly alike, and there are a variety of room types which differ significantly in shape and size. The client’s program called for a specific number of suite options, rooms with and without balconies and fireplaces, rooms with bath tubs and others with walk-in showers. ADA requirements called for wheelchair accessibility in a percentage of rooms. The irregular ‘H’ shape of the guest floor footprint, and various program requirements meant the rooms would not be the same size and shape. Instead, the design of each room was approached individually, which in turn led to highly customized prefabrication of the walls.
Roof Construction | Designing the roof for prefabrication was also a challenge. The teams had to design within pre-approved height restrictions and an irregular ‘H’ shape footprint. The pool deck cuts into the roof structure in places and other portions of the roof had to be designed to accommodate mechanical equipment carefully hidden from view of guests.
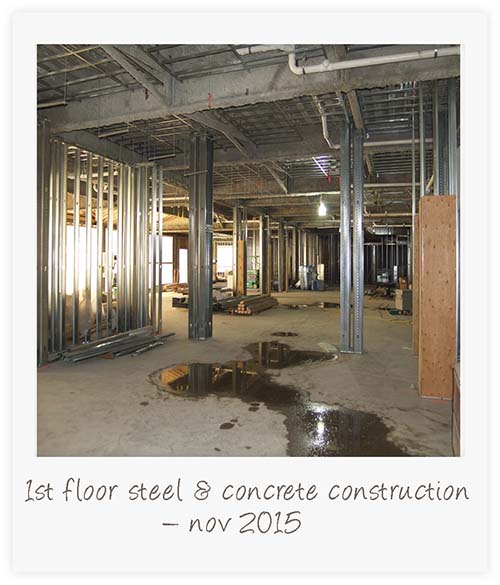
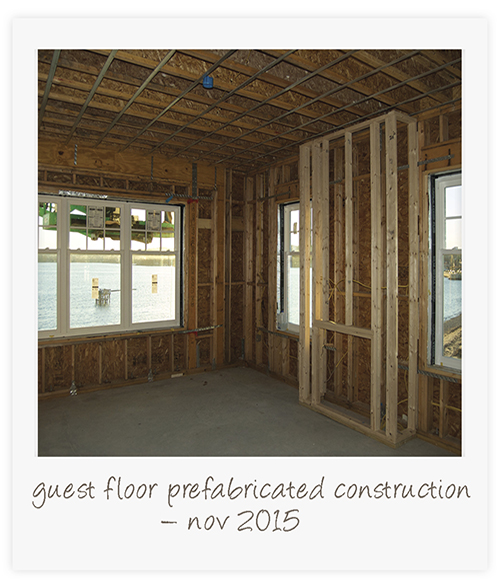
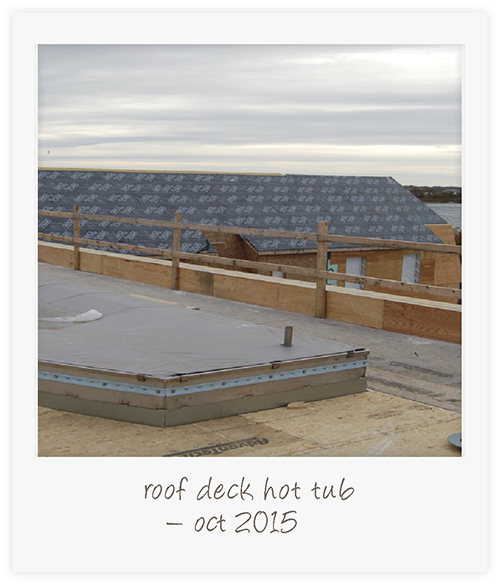
HVAC INTEGRATIONS
The designers chose a VRF (variable-refrigerant flow) system to provide heating and cooling for the hotel. This system consists of lower floor energy-recovery ventilators (ERVs) and ducted VRF units, and rooftop mounted ERVs serving individual guest floor terminal units. All VRF condensers, make-up air units, and kitchen exhausts are on the roof.
This system, with internally located terminal units at guest rooms, allowed OL+ to provide larger windows and doors at the exterior walls (by avoiding fan/coil units at these locations). The internally located units allowed for a greater complexity of roof shaping, elimination of exterior wall grilles, and a more traditional and attractive exterior. In addition, the elimination of wall-mounted units allows guests to walk right up to exterior walls to enjoy the view. The deliberate concealing of the terminal units gives these rooms have an airy and open feel, with plenty of light.
The VRF system allows for maximum control and functionality, and increased energy- efficiency compared to other systems.
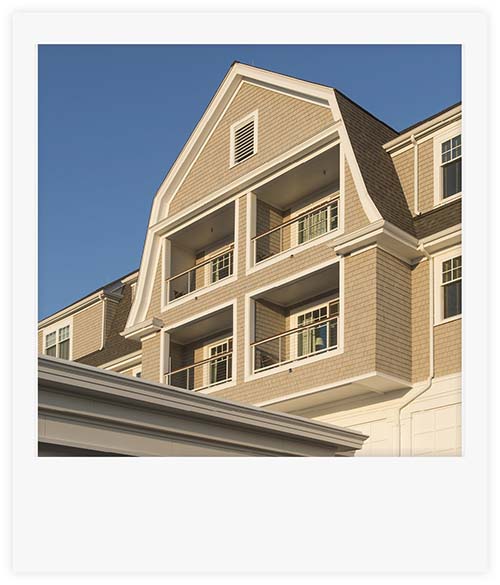
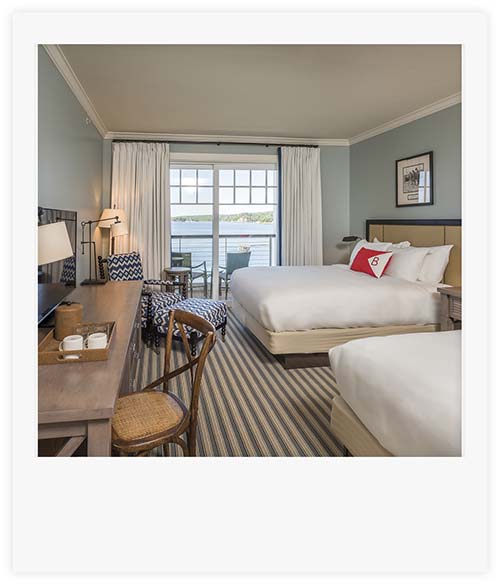
KITCHENS & CATERING
John’s extensive knowledge of the hospitality design meant that he understood the requirements of both the public space as well as the functionality of the all-important ‘back of the house’ spaces. The client’s desire was to create a nautically themed waterfront hotel, with conference/function/wedding facilities, and an upscale bar and restaurant catering to hotel guests and members of the public alike.
Recognizing the large volume of food production required to meet these needs (plus room service for 94 rooms), John suggested including a smaller kitchen at the east in addition to the main kitchen at the west. This second kitchen is dedicated solely to the catering of private events and weddings, a mainstay of the client’s business. Event rooms are positioned on the south of the building to take advantage of the best ocean views. At the back of the house, to the north, the kitchens are located on opposite ends of a connecting corridor overlooking Commercial Street and hotel parking.
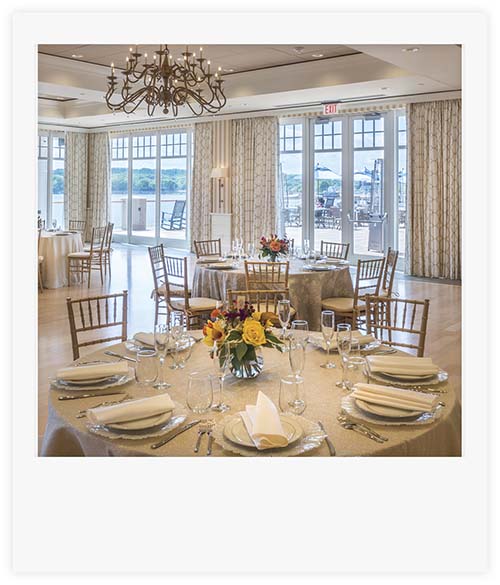
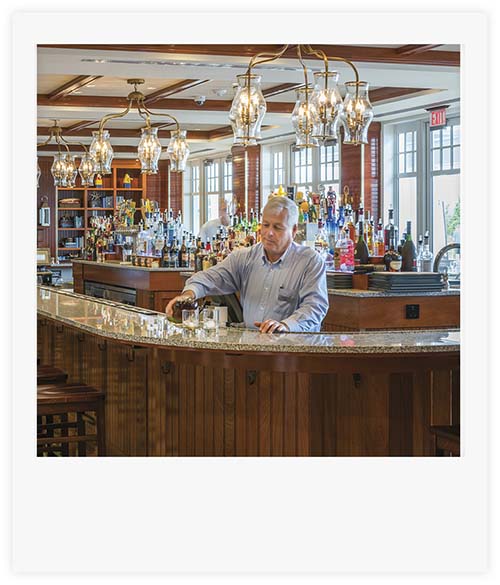
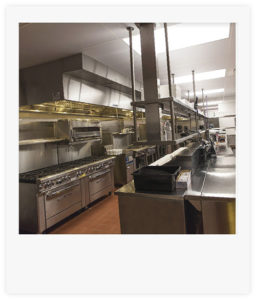
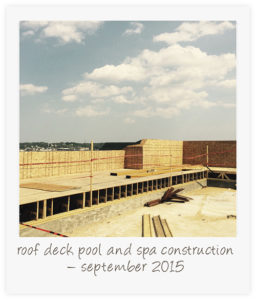
ROOF DECK POOL & HOT TUB
Although the client initially imagined locating the pool at the first floor deck, John realized that this would limit the amount of entertainment space on the deck, and would create an unmanageable mix of formal and informal activities that would be better separated. With this in mind, the team located the pool, hot tub and a bar on the roof, increasing the overall gathering space available to the hotel.
The rooftop location, however, presented many engineering challenges, including the need for additional steel structure from the ground up to support the added weight of the pool and spa. The team at OL+ created a roof deck layout that masked the mechanical equipment and maintained the all-important water views. Mechanical equipment set low within into the roof volume, shielded from view by the sloping portions of the upper roof. East and west walls between the mechanical equipment and the pool deck are finished with cedar shingles, in keeping with the rest of the exterior of the hotel.
The payoff was worth the extra effort; the rooftop deck is an exclusive destination for hotel guests, complete with bar, infinity pool, spa, and both ocean and harbor views.
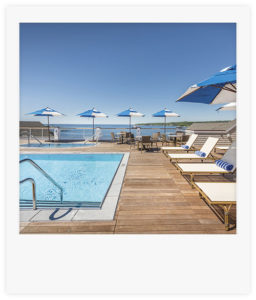
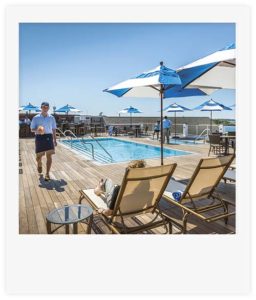
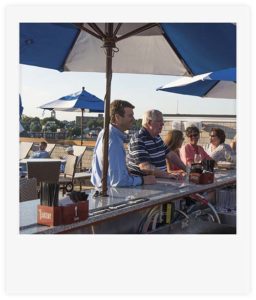

A Collaborative Success
The Beauport Hotel’s design required innovative solutions to manage structural demands, coastal site challenges, and complex programming needs. OLSON LEWIS + Architects worked closely with Windover Construction and all project partners to deliver a destination hotel that honors Gloucester’s maritime heritage while offering guests a modern, luxurious experience.
Designing the floor plan within a zoning envelope previously approved by the city of Gloucester presented some challenges, which John and the team at OL+ skillfully overcame. The design/build, fast-track project delivery process required close collaboration between the OL+ and Windover Construction (the hotel’s Design Build Construction Manager).
A hybrid steel/concrete/wood structural system was used to construct the building. The assembly comprises steel framing with concrete slabs at the ground and first floors, and prefabricated wood framing for the second and third floors and roof structure. Steel framing supports the rooftop pool and tower roof. The OL+ team worked collaboratively with all project partners to overcome any obstacles, balancing the needs and concerns of multiple constituents with budget and scheduling constraints.
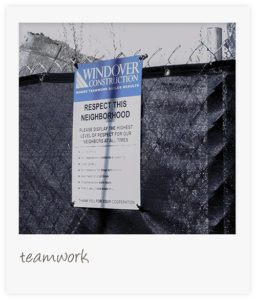
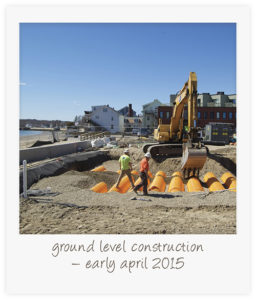
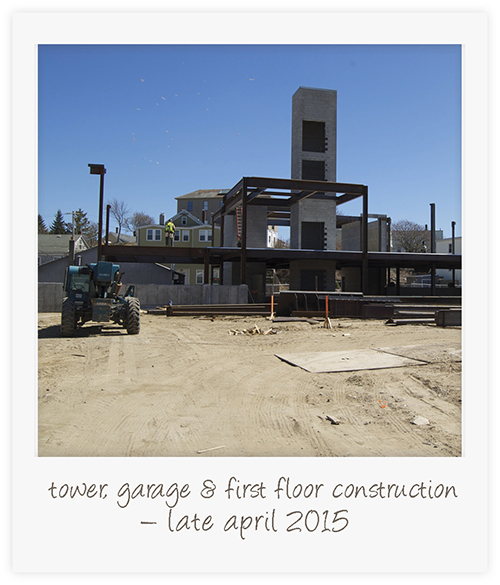
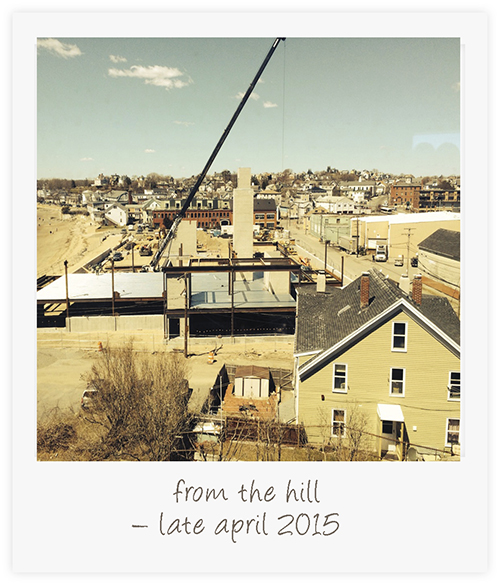
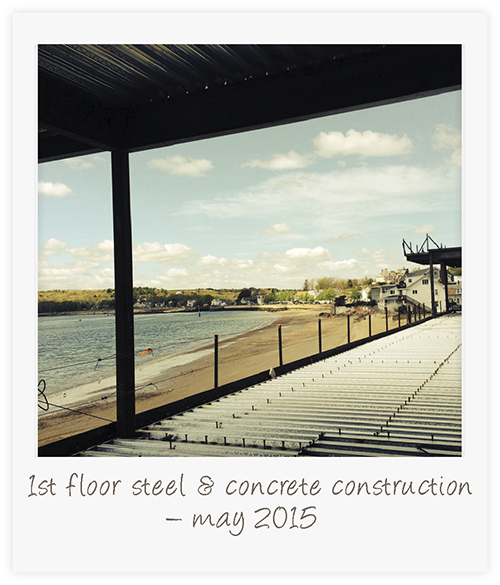
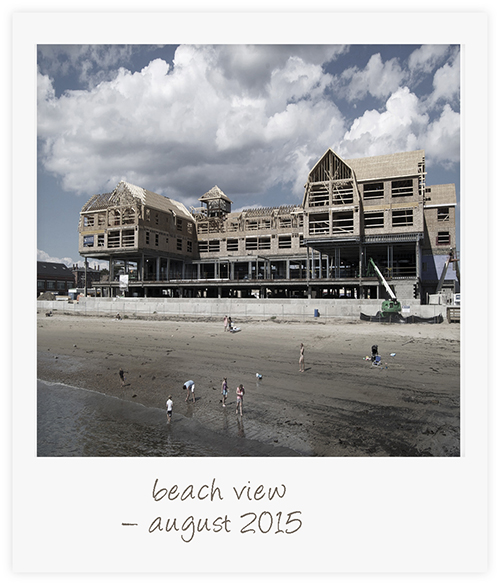

HURRICANE & FLOODING CONCERNS
The coastal Massachusetts waterfront location presented both flooding and hurricane concerns. A concrete sea wall at garage level was constructed to help resist coastal flooding during a storm surge, and primary public spaces were elevated to first floor level. At the first floor deck, ten-foot-high doors and windows were manufactured by a Florida-based company that specializes in impact-resistant coastal applications. In the guest rooms, vinyl-framed impact-resistant windows and sliding doors tested to withstand hurricane-force weather allow plenty of light into the rooms.
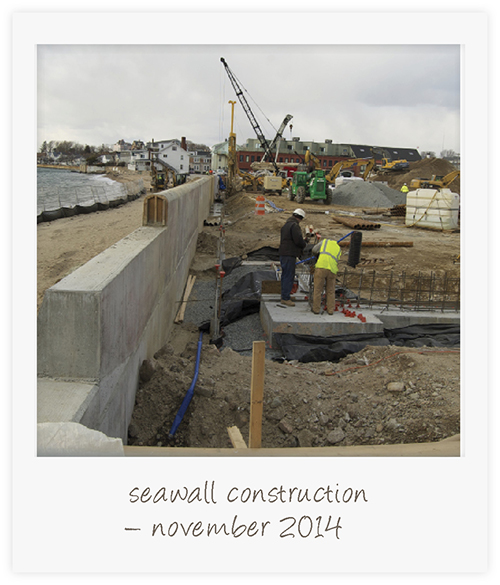
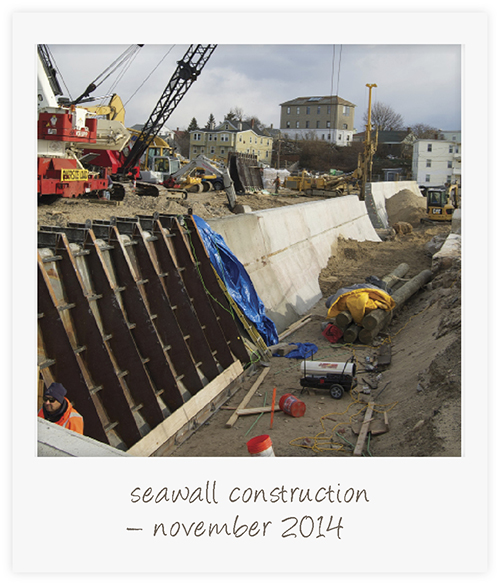

CUSTOMIZED PREFABRICATED CONSTRUCTION
The hybrid construction system employed for the project provided a number of benefits. Off-site construction of the wood framing and roof trusses was vital for keeping the project both on budget and on schedule. The use of prefabricated framing on the upper levels allowed for concurrent sequencing of major structural systems, which would have been impossible using more conventional construction methods.
Second and third floor framing was factory-fabricated while ground and first floor steel was being erected on site. The second floor concrete slab was the first to be poured. The wood framing was erected from the second floor up, while the remaining slabs below were poured. As third floor walls were being erected, roof trusses were fabricated, making them ready to install as walls were completed. Concurrent with this, first floor light-gage metal exterior wall framing, and steel stud interior framing went into place.
The prefabricated wood framing is computer designed to accommodate the irregular shape of the building footprint, gambrel roofs with third floor dormers, and a complex upper roof which is home to an exterior deck with pool, and recessed wells housing mechanical equipment. Prefabrication of the wood framing allowed greater control over the building configuration, and helped reduce construction materials crowding on the very tight Gloucester building site. It was also helpful in limiting construction waste. Throughout the process, the team worked closely with Boise Cascade, the wood framing prefabricator. Boise is a company that adheres to responsible environmental stewardship and sustainability practices, which was important to the entire team.
Guest Floor Construction |Although many of the rooms on the second and third floors are similar, few are exactly alike, and there are a variety of room types which differ significantly in shape and size. The client’s program called for a specific number of suite options, rooms with and without balconies and fireplaces, rooms with bath tubs and others with walk-in showers. ADA requirements called for wheelchair accessibility in a percentage of rooms. The irregular ‘H’ shape of the guest floor footprint, and various program requirements meant the rooms would not be the same size and shape. Instead, the design of each room was approached individually, which in turn led to highly customized prefabrication of the walls.
Roof Construction | Designing the roof for prefabrication was also a challenge. The teams had to design within pre-approved height restrictions and an irregular ‘H’ shape footprint. The pool deck cuts into the roof structure in places and other portions of the roof had to be designed to accommodate mechanical equipment carefully hidden from view of guests.
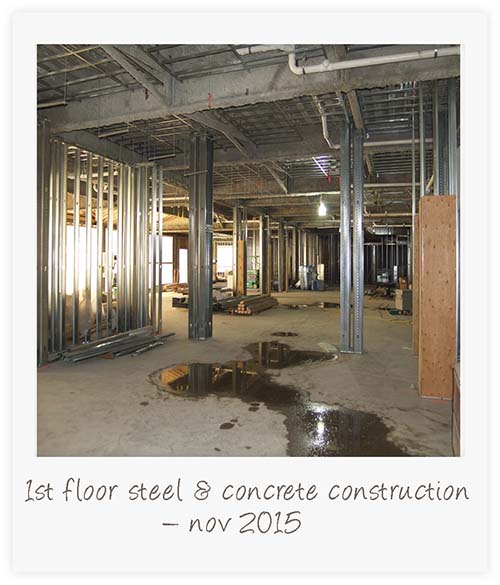
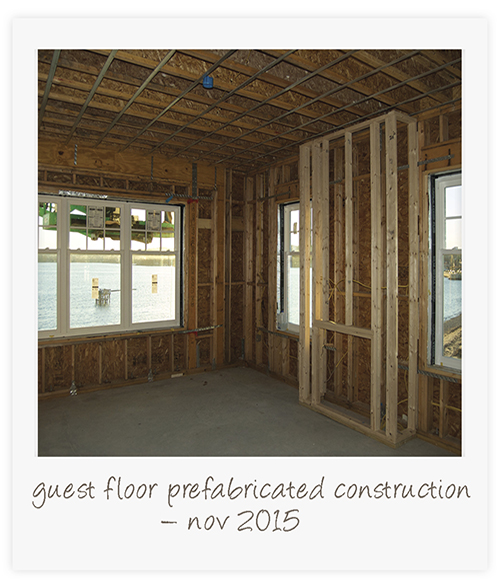
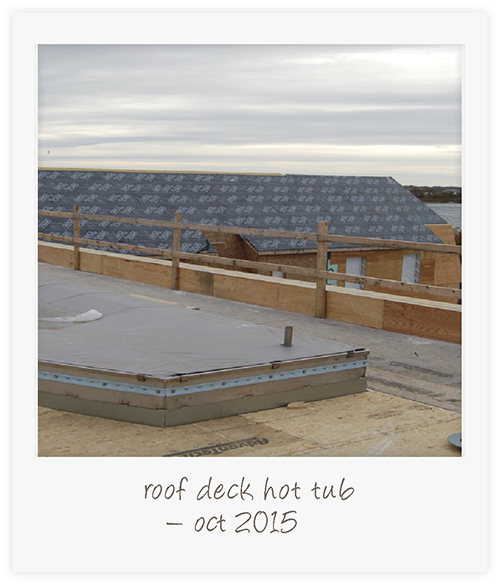
HVAC INTEGRATIONS
The designers chose a VRF (variable-refrigerant flow) system to provide heating and cooling for the hotel. This system consists of lower floor energy-recovery ventilators (ERVs) and ducted VRF units, and rooftop mounted ERVs serving individual guest floor terminal units. All VRF condensers, make-up air units, and kitchen exhausts are on the roof.
This system, with internally located terminal units at guest rooms, allowed OL+ to provide larger windows and doors at the exterior walls (by avoiding fan/coil units at these locations). The internally located units allowed for a greater complexity of roof shaping, elimination of exterior wall grilles, and a more traditional and attractive exterior. In addition, the elimination of wall-mounted units allows guests to walk right up to exterior walls to enjoy the view. The deliberate concealing of the terminal units gives these rooms have an airy and open feel, with plenty of light.
The VRF system allows for maximum control and functionality, and increased energy- efficiency compared to other systems.
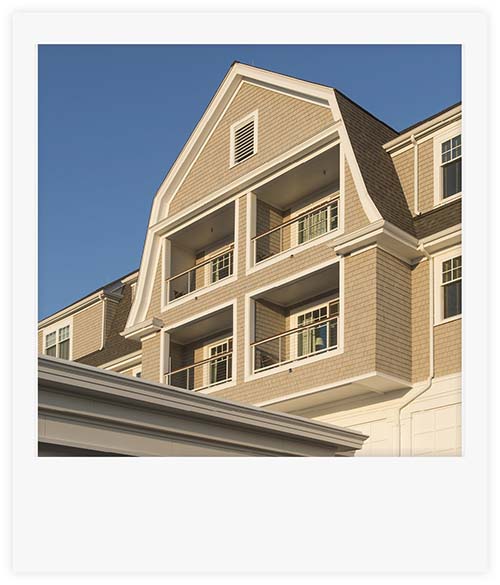
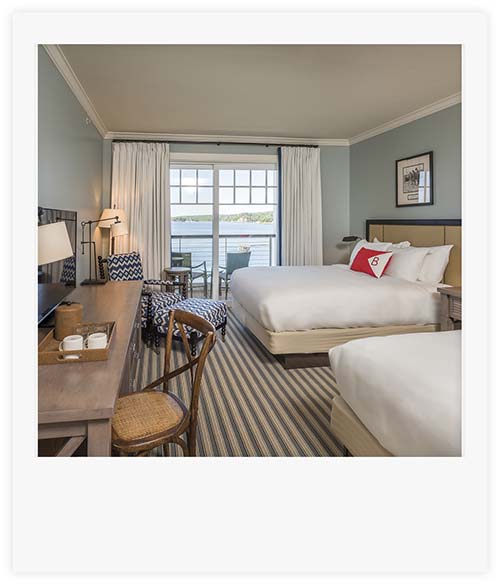
KITCHENS & CATERING
John’s extensive knowledge of the hospitality design meant that he understood the requirements of both the public space as well as the functionality of the all-important ‘back of the house’ spaces. The client’s desire was to create a nautically themed waterfront hotel, with conference/function/wedding facilities, and an upscale bar and restaurant catering to hotel guests and members of the public alike.
Recognizing the large volume of food production required to meet these needs (plus room service for 94 rooms), John suggested including a smaller kitchen at the east in addition to the main kitchen at the west. This second kitchen is dedicated solely to the catering of private events and weddings, a mainstay of the client’s business. Event rooms are positioned on the south of the building to take advantage of the best ocean views. At the back of the house, to the north, the kitchens are located on opposite ends of a connecting corridor overlooking Commercial Street and hotel parking.
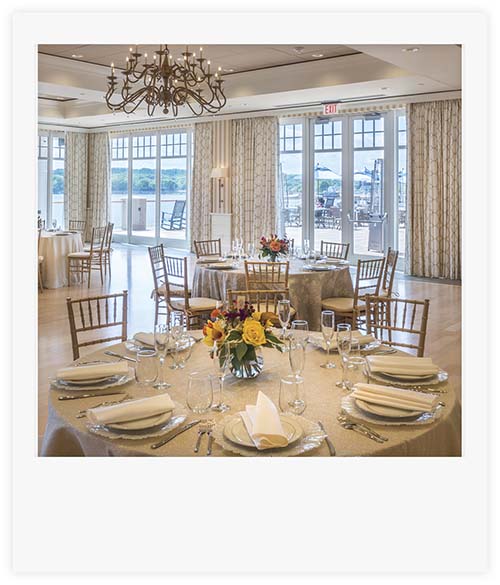
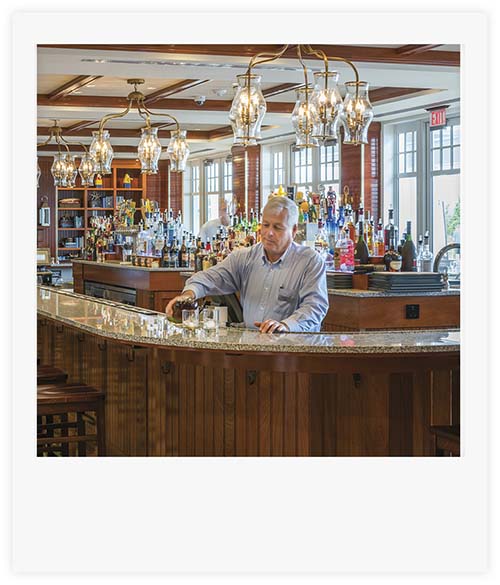
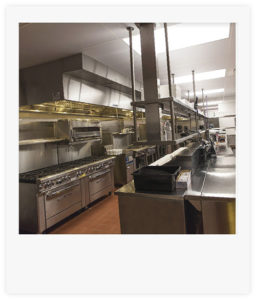
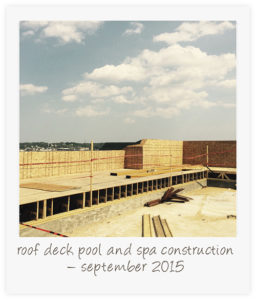
ROOF DECK POOL & HOT TUB
Although the client initially imagined locating the pool at the first floor deck, John realized that this would limit the amount of entertainment space on the deck, and would create an unmanageable mix of formal and informal activities that would be better separated. With this in mind, the team located the pool, hot tub and a bar on the roof, increasing the overall gathering space available to the hotel.
The rooftop location, however, presented many engineering challenges, including the need for additional steel structure from the ground up to support the added weight of the pool and spa. The team at OL+ created a roof deck layout that masked the mechanical equipment and maintained the all-important water views. Mechanical equipment set low within into the roof volume, shielded from view by the sloping portions of the upper roof. East and west walls between the mechanical equipment and the pool deck are finished with cedar shingles, in keeping with the rest of the exterior of the hotel.
The payoff was worth the extra effort; the rooftop deck is an exclusive destination for hotel guests, complete with bar, infinity pool, spa, and both ocean and harbor views.
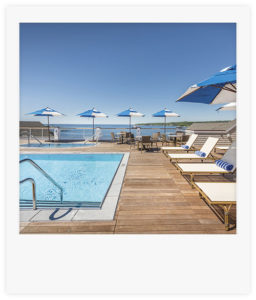
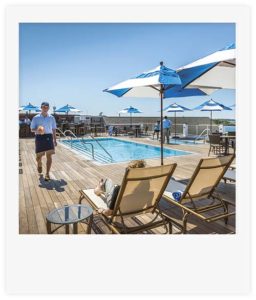
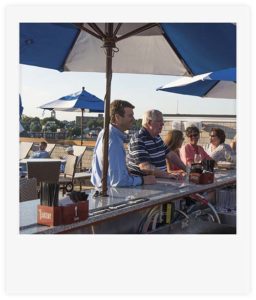

A Collaborative Success
The Beauport Hotel’s design required innovative solutions to manage structural demands, coastal site challenges, and complex programming needs. OLSON LEWIS + Architects worked closely with Windover Construction and all project partners to deliver a destination hotel that honors Gloucester’s maritime heritage while offering guests a modern, luxurious experience.